KEEPING UP IN LOCKDOWN
- teamseventyone
- Apr 6, 2021
- 8 min read
Updated: Apr 8, 2021
It’s been hard to find the time together for us to finish the bikes during the COVID crisis. The progress of our rebuild was a lot slower than we intended. There were issues with transportation and deliveries that slowed everything down and Ritchie and I could only work together at weekends, due to our own working commitments from home. So, as you can imagine it’s been a slow process, but at least we got there with one of the bikes – the ZX10-R.

At long last, Ritchie on track to test the Wössner-powered ZX10-R – in its blue practice clothes for now…
Some of the work on the engine relied upon outside help before we could complete the engine rebuild, so we only just completed the bike for its first test day at Brands Hatch over the Easter weekend.

All set and raring to go, but it was so cold at Brands Hatch first thing in the morning, we had to put its socks on...
Anyway, this is what we did and where we are now.
Well, the first big news for us was from German manufacturer, Wössner Performance Pistons who supplied us with a piston kit free of charge to refresh our engine! They turned up via their newly opened office here in the UK. They have made a big name for themselves in car racing, drag racing and motocross and were very keen to get involved with us in the UK motorcycle racing scene.

Massive support for us from Wössner in Germany, who supplied us with a piston kit FOC!
So, the first job was to whip the engine out and split the crankcase halves, get rid of the old pistons and check the crank’s bearing shells and big end shells. We couldn’t see the colour coding on the old shells so there was a lot of measuring with different sizes to be absolutely certain we were buying the correct size. This meant a lot of assembling and reassembling of the crankcase halves, and on-and-off with the conrods. Still, we got there in the end.

Measuring, bolting up and measuring again…then we had to wait a week for the parts to turn up. It all takes time.
Once we were happy with that, we took the cylinders to our good friends at Roland Alsop to hone the Nikasil bores which they did quite quickly for us.
Unfortunately, we then had to wait until well after Christmas to get our cylinder head back in time to do all the valve timing and valve clearances. At that point we realised that you can’t reuse titanium valves by lapping them in for another term. What a blow that was, more expense that we hadn’t budgeted for!
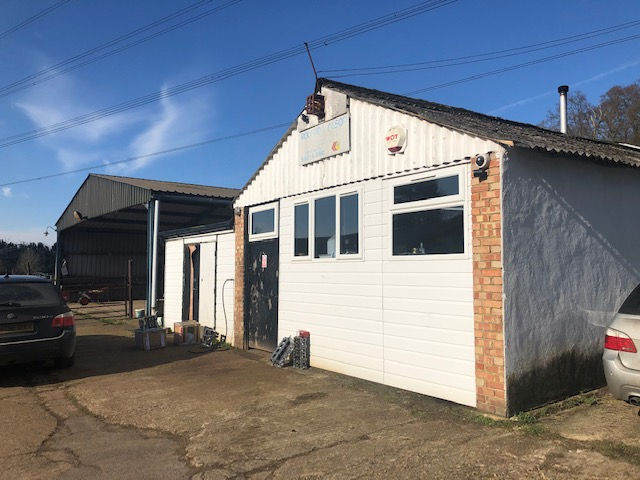
Roland and Alsop honed the Nikasil bores and carried out most of the cylinder head work for us…
Anyway, Ritchie looked at the cost of some new valves from Kawasaki and they were working out a bit expensive even with a discount that he’d negotiated. He then told me that Vance &Hines do a titanium valve for the ZX10-R, so I contacted them at the UK office, who told me I needed to speak to someone in the USA. After contacting them in California they directed me to the ‘Raceshop’ in Ohio, Indiana.
I spoke to a guy named Craig, who said he had a set of valves in stock and would be happy to help us on cost with a deal that was going to save us quite a lot of money. We were so pleased that he was willing to sponsor us all the way from America.

Nice new titanium valves ready to drop into the cylinder head.
They were despatched the next day, but UPS lost them when they got to the distribution hub in England, so we had to wait for an inquiry which took nearly two weeks. Then they turned up at our local depot and were finally delivered, very late. Even then, I had to chase the delivery driver to his van who had just stuck a bill for import duties through the door - even though I had paid them - and didn’t even ring doorbell! We almost lost them again! Well, better late than never and we were able to get on with the valve timing and measuring valve clearances now that the cylinder head was back from the engineers.
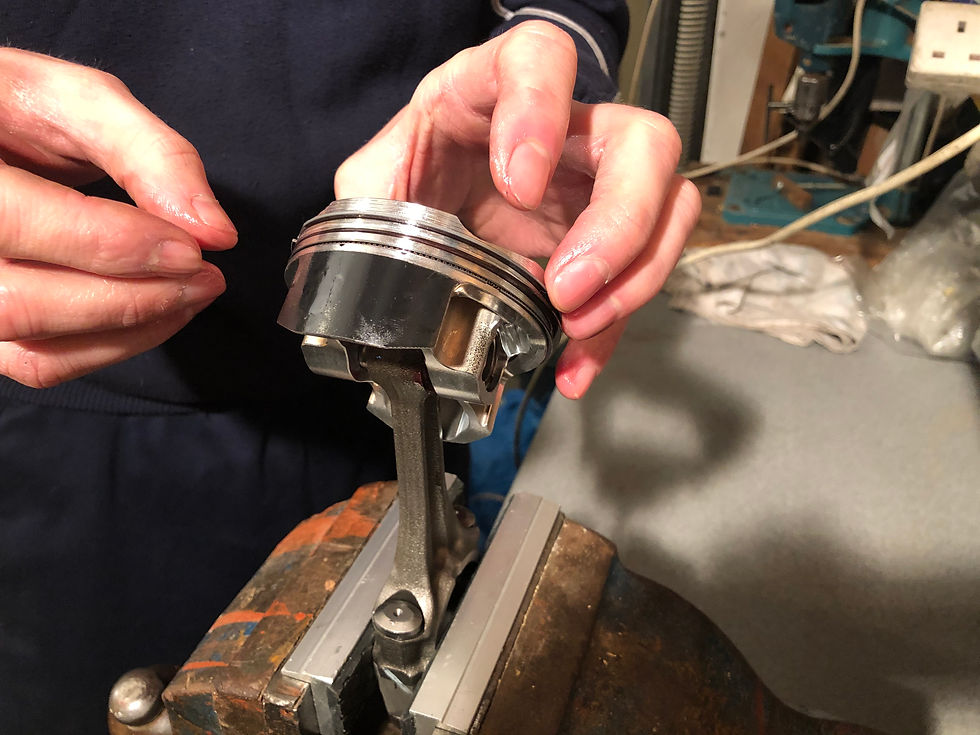
Ritchie fitting the rings to the Wössner high-performance pistons.
Back to installing the pistons, once the bores were honed, Ritchie gapped all the rings and we fitted them to the conrods ready to drop into the bores. On the ZX10-R, the way the engine splits, you have to drop the pistons in from the top…oil rings first, which is a bit tricky. Anyway, we put plenty of oil around them and they slid in just fine.

The Fantastic Four…superpower for a superbike from Wössner …
Once that was done, we could put the new big end shells in and tighten it all up with brand new conrod bolts.
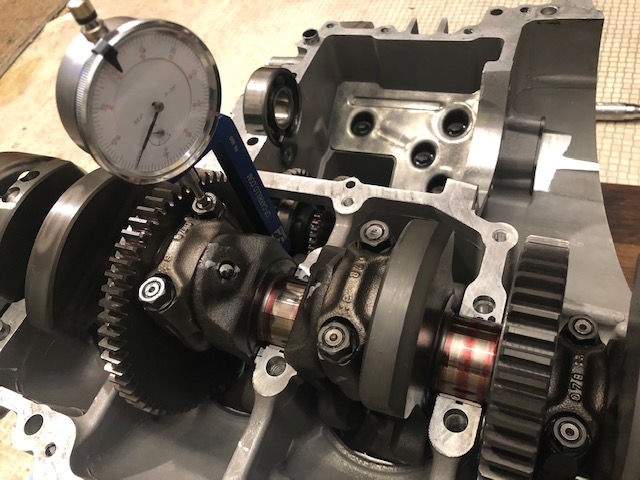
Measuring the stretch with a gauge is more accurate than a torque wrench when tightening the conrod bolts...
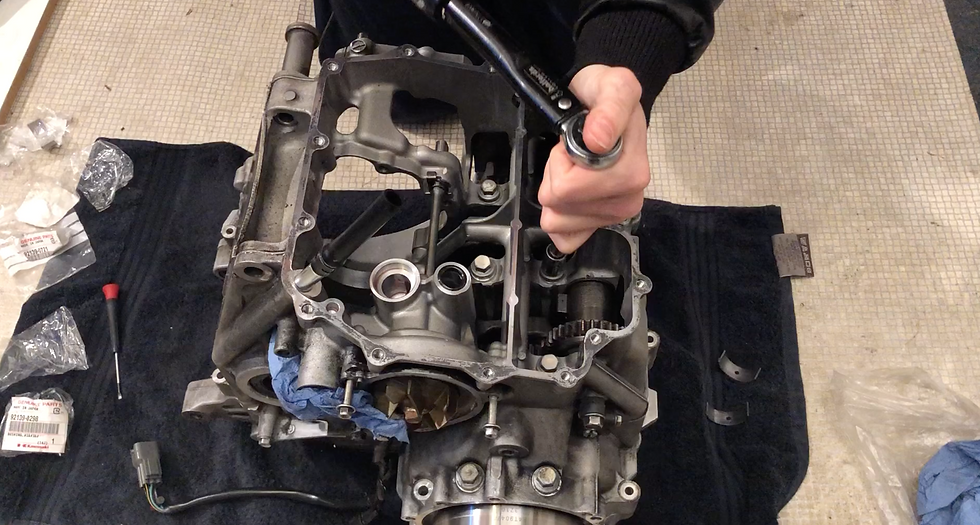
Out with the torque wrench again to put the crankcase halves together for the final time...

Pistons in place, all bolted up and ready for the cylinder head…
With everything turning nicely at the bottom end, it was time to turn our attention to the top end. While all this was going on we shipped the cams off to Kent Cams for some work to be done and asked Roland and Alsop if they could flow the inlet and exhaust ports for us.
They did a good job too. But we had to wait quite a while for this job to be done so we turned our attention to our ZX7-R. We know this one inside out now, but it still took a bit of time once we had the engine out and measured everything up to check shells and shims. We also stripped it down to the frame, removing the swingarm and suspension units that needed a service and a check over after the big crash at Donington to make sure everything was straight. All was good, thank goodness!

Bare to the bone, our ZX7-R being prepared for a comeback after the terrible crash at Craner Curves, Donington, almost destroyed it.
Well, back to the ZX10-R, and once we got everything back from Roland and Alsop and Kent Cams, Ritchie set about the valve timing and measuring piston clearance with the new valves in place.
Once he was happy with the valve to piston clearance, he could work out how much to skim off the head for more compression. It says in the race manual that you take 0.4mm off, but he decided to play safe and remove only 0.2mm – which is still quite a lot!

Freshly skimmed head with new Vance and Hines valves, it looks like a piece of art!
Finally, a light clean-up of the valve seats and with the new valves installed everything could now go back on top of the engine for the last time. One last thing to do was carry out a final check of the valve timing and all was ready for the motor to go back into the frame ready for running in. We used Miller mineral oil for running in the engine, supplied by our loyal sponsor Opie Oils … they’ve been fantastic and have always been ready to supply us in good time with everything we need.

We turned our ZX10-R into a streetfighter to run it in…
After about 3 hours of running time, we carried out a leak test and were very happy that the Wössner rings had mated and bedded in well with the Kawasaki bores.
Ritchie had been speaking to Matt at TBR Performance about fine tuning the bike and decided to book a couple of hours on his Dyno.
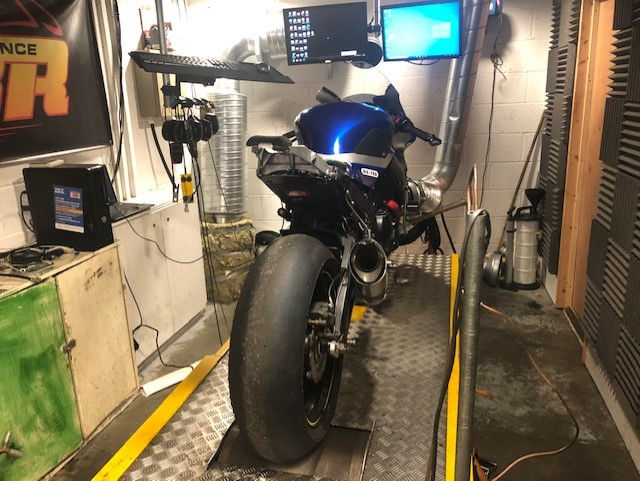
All hooked up and ready for a run on the dyno with TBR Performance in Hungerford.
It was good to see just on the first run that the peak power had increased from where it used to be from 181bhp to 196bhp! With a bit of tweaking here and there Matt improved the overall performance and boosted it up to 198.6bhp. As Ritchie was aiming for 195bhp he was very pleased with all the hours we’d spent on the bike to achieve higher peak power. Matt reckons that the exhaust is holding back the power and if we could fit – and afford – a 65mm system, it would go to over 200bhp!
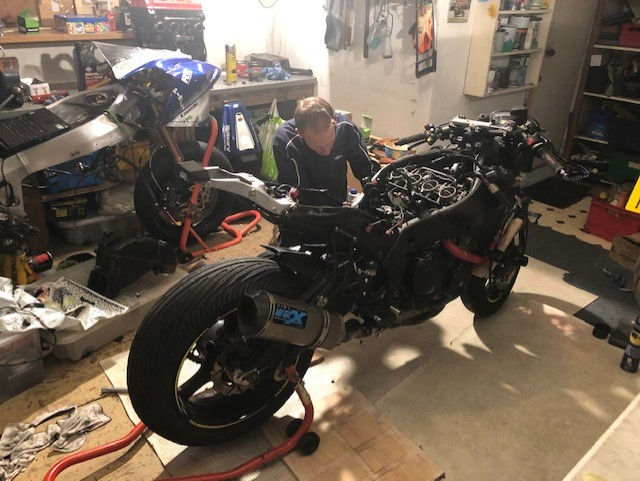
Fitting the throttle cables for the auto blip mechanism was a bit fiddly at times…
Back in the garage a week later, we fitted an auto-blipper to automatically blip the engine for the downshifting. We had a bit of trouble with this at first, it wasn’t easy to fit and the cables it comes with are unusable. We had to make our own up from a couple of second-hand Kawasaki cables.

Auto blip solenoid fits snug in the tail section under the seat…
It all takes time and that wasn’t the only thing; the instructions were poorly translated from Italian. This meant we couldn’t get the unit to work properly, but after Ritchie contacted the manufacturer – they were actually very helpful – he was able to program it to work and blip the engine.
After a few more refinements to the throttle assembly, we were ready to go to Brands Hatch to put it through a final, nail-biting, day’s testing.
Brands is one of Ritchie’s favourite circuits and thanks to Bemsee, who’d organised a test day to come back after COVID lockdown, it was a good place to start after such a long time away from riding a race bike.

A cold start with track temperature at only 8˚, but things warmed up later to around 24˚…
I was amazed that Ritchie seemed to click straight away with the bike, after the first session he came in smiling saying that he felt like he’d never been away from it. His lap times proved it too, as he was just a second off a good race pace by lunchtime. There were a few adjustments he had to make to the auto-blipper, but by the afternoon he had the bike pretty much set up. The only thing stopping him going any faster was the rear tyre which was completely worn out for the last two 15-minute sessions. Ritchie said it felt like riding on a flat; the tyre had worn evenly, but the wear markers had completely disappeared, and the bike was starting to slide and become hard to keep settled.
For the rest of the day, he concentrated on getting the bike to keep turning through the corners rather than focussing on pace, although he still popped in the odd fast lap when he had a clear run.
Overall, it was a great day, cold to start with but with the sun out at about 11 o’clock onwards it was a very pleasant day to return to the circuit and give the bike a good run.
Next time out we’ll be going up to Oulton Park in Cheshire to take part in practice and then a race meeting the following day with the Wirrall 100 Club. We’ll let you know how we get on!
Big thanks to all our other sponsors close to home: The continued and much-valued support from Opie Oils (with two bikes to look after this is a real bonus) Cradley Kawasaki, Maxton, R&G and Chris Cowan from Loomies Motorcycle Accessories and Clothing Shop who came along with the offer of a new set of Held custom leathers for Ritchie. We hope they’ll be ready for the first round of Powerbikes in May.
See you all soon.
Bernie Thornton TEAM 71
Comments